In metal water bottle manufacturing, your quality control is crucial for durability and customer satisfaction. Ensure stringent procedures for safety and high standards. Source materials from reputable suppliers, inspect for integrity, and collaborate for quality. Monitor production processes with automation and real-time analysis. Test for durability and safety to prevent harm. Regularly check for defects, train staff for detection, and act promptly on corrections. Adhere strictly to industry standards for brand reputation. Remember, attention to detail in quality control will strengthen your market position and customer trust.
Key Takeaways
- Regular audits of material sourcing for integrity and compliance with industry standards.
- Implement automated production monitoring with real-time analysis for optimization.
- Conduct thorough durability and safety testing to ensure product quality.
- Train staff for defect detection, root cause analysis, and prompt corrective actions.
- Adhere to industry standards through regular audits, employee training, and quality control checks.
Importance of Quality Control
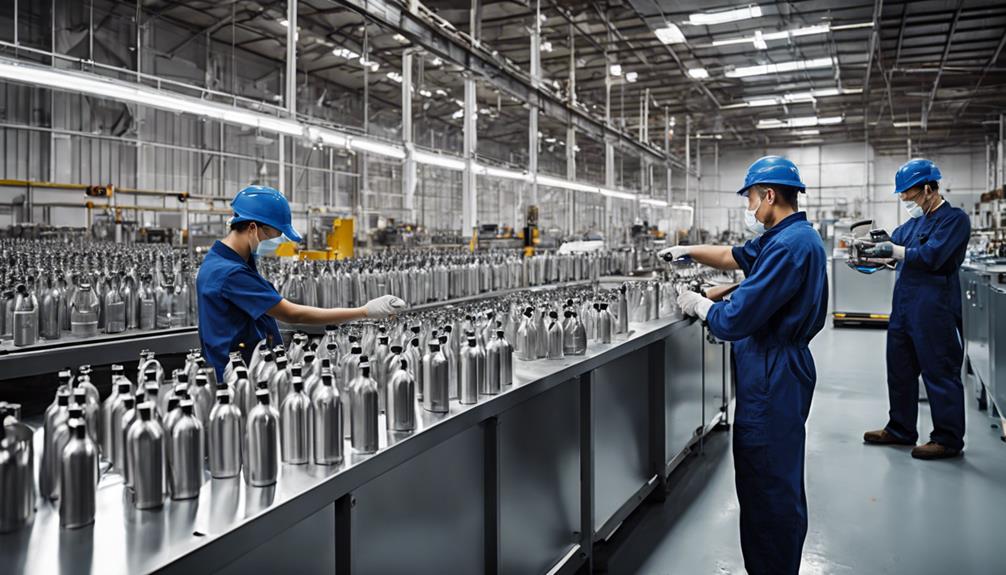
Implementing robust quality control measures in the manufacturing of metal water bottles is crucial for ensuring customer satisfaction and maintaining a strong brand reputation. By meticulously inspecting every stage of production, from raw materials to final product assembly, you can guarantee that each water bottle meets the highest standards of quality and durability.
Quality control plays a vital role in enhancing customer satisfaction by delivering products that are free from defects and meet or exceed expectations. By consistently producing high-quality metal water bottles, you can build trust with your customers and establish a loyal consumer base. This, in turn, leads to positive reviews, repeat purchases, and increased brand loyalty.
Moreover, maintaining stringent quality control processes safeguards your brand reputation. By preventing substandard products from reaching the market, you demonstrate your commitment to excellence and reliability. This dedication to quality not only attracts new customers but also solidifies your standing in the market as a reputable manufacturer of metal water bottles.
Material Sourcing and Inspection
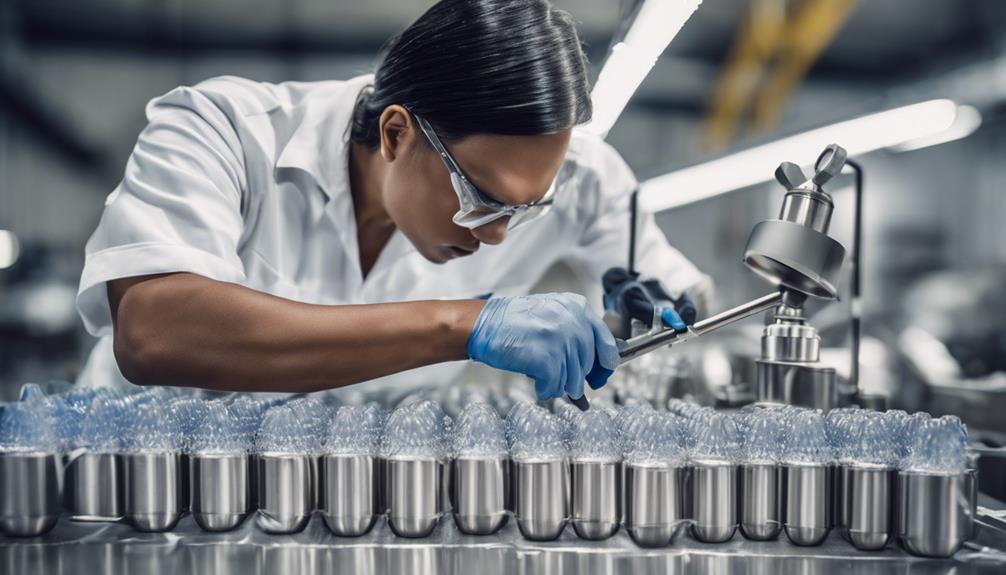
You need to meticulously assess the raw material quality to ensure your metal water bottles meet industry standards.
Conduct thorough supplier certification checks to guarantee reliability and consistency in your materials.
Outline a detailed inspection process to maintain product integrity throughout manufacturing.
Raw Material Quality
Ensuring the high quality of raw materials for metal water bottle manufacturing involves meticulous sourcing and rigorous inspection processes. Quality assurance begins with selecting reputable suppliers who adhere to industry standards. When evaluating potential suppliers, consider their manufacturing techniques to ensure they align with your quality requirements.
Inspecting raw materials is a critical step in the production process. Implement thorough quality checks to verify the material's integrity and suitability for manufacturing. Conduct tests to assess factors like durability, corrosion resistance, and material composition. Any deviations from the specified standards should prompt immediate corrective action.
Regular audits of suppliers can help maintain consistent material quality. By monitoring their processes and performance, you can address any issues promptly and prevent disruptions in production. Collaborate closely with suppliers to communicate expectations and optimize material quality.
Supplier Certification Checks
To ensure the quality and reliability of raw materials for metal water bottle manufacturing, conducting thorough supplier certification checks is paramount. When it comes to material sourcing and inspection, certification audits play a crucial role in maintaining high standards.
Here are four key steps to consider:
- Verify Certification Authenticity:
- Always confirm that the supplier's certifications are legitimate and up to date. This step ensures that the materials meet the required quality standards.
- Check for Compliance:
- Scrutinize whether the supplier's practices align with industry regulations and standards. This examination guarantees that the materials are sourced ethically and responsibly.
- Assess Quality Assurance Processes:
- Evaluate the supplier's quality assurance procedures to guarantee consistency in the materials provided. This assessment helps in preventing defects and ensuring product reliability.
- Establish Communication Channels:
- Maintain open communication with suppliers to address any concerns promptly. Building a strong relationship facilitates resolving issues and maintaining quality standards throughout the manufacturing process.
Inspection Process Details
When sourcing materials for metal water bottle manufacturing, a detailed inspection process is vital to ensure the quality and reliability of the raw materials. To maintain the integrity of the production line, thorough inspections are conducted to prevent defects from entering the manufacturing process.
Automated inspection systems play a crucial role in this phase, providing a high level of quality assurance by quickly identifying any potential issues with the materials.
Automated inspection processes are designed to meticulously analyze the sourced materials, checking for any imperfections or deviations that could impact the final product. By utilizing advanced technology, manufacturers can proactively address any concerns before they escalate, ensuring that only materials meeting the highest standards are used in the production of metal water bottles.
Incorporating automated inspection into the material sourcing phase not only enhances the overall quality of the end product but also streamlines the manufacturing process by reducing the likelihood of defects and rework. This proactive approach to quality control sets the foundation for producing durable and reliable metal water bottles that meet customer expectations.
Production Process Monitoring
Monitoring the production process of metal water bottle manufacturing involves real-time data collection and analysis to ensure quality and efficiency. To effectively monitor the production process, consider the following steps:
- Automated Monitoring Systems: Implement automated sensors and monitoring devices throughout the production line to track key parameters such as temperature, pressure, and material flow in real time.
- Real-Time Analysis Software: Utilize advanced software systems that can process data instantaneously, allowing for quick identification of any deviations from the set quality standards.
- Quality Assurance Checks: Conduct regular quality checks at various stages of the production process to verify that the bottles meet the required specifications and standards.
- Process Optimization Strategies: Continuously analyze the production data to identify bottlenecks or inefficiencies in the manufacturing process, enabling you to make proactive adjustments for improved productivity and quality assurance.
Testing for Durability and Safety
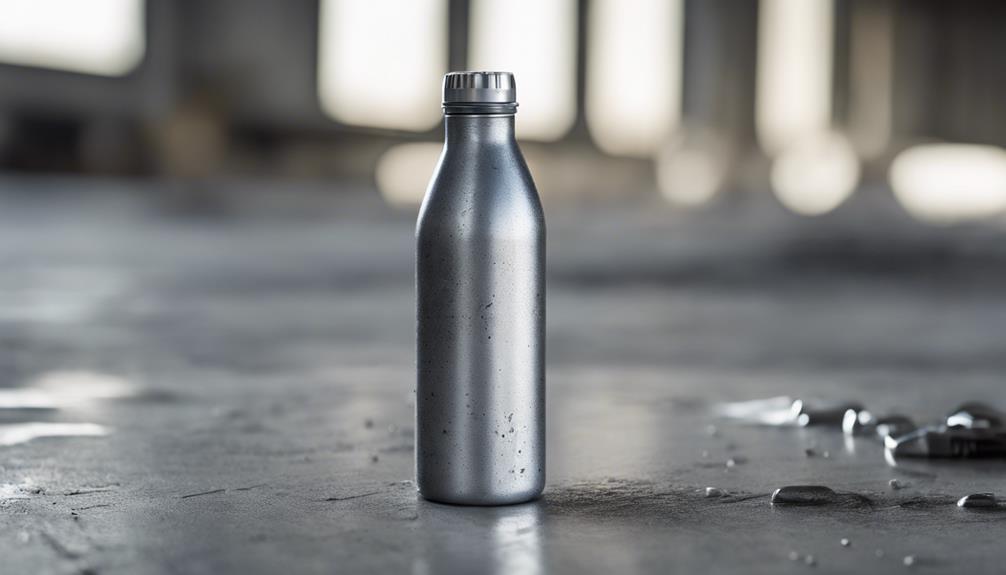
For ensuring the quality and safety of metal water bottles, thorough testing procedures for durability and safety are imperative in the manufacturing process. Durability testing involves subjecting the metal water bottles to simulated conditions, such as drops, temperature changes, and pressure tests, to ensure they can withstand everyday use without compromising their structural integrity.
Safety standards play a crucial role in verifying that the materials used in the manufacturing process don't pose any health risks to consumers. These standards encompass factors like checking for harmful chemicals, ensuring proper insulation to prevent burns, and verifying that the bottles are free from sharp edges that could cause injury.
Defect Detection and Correction
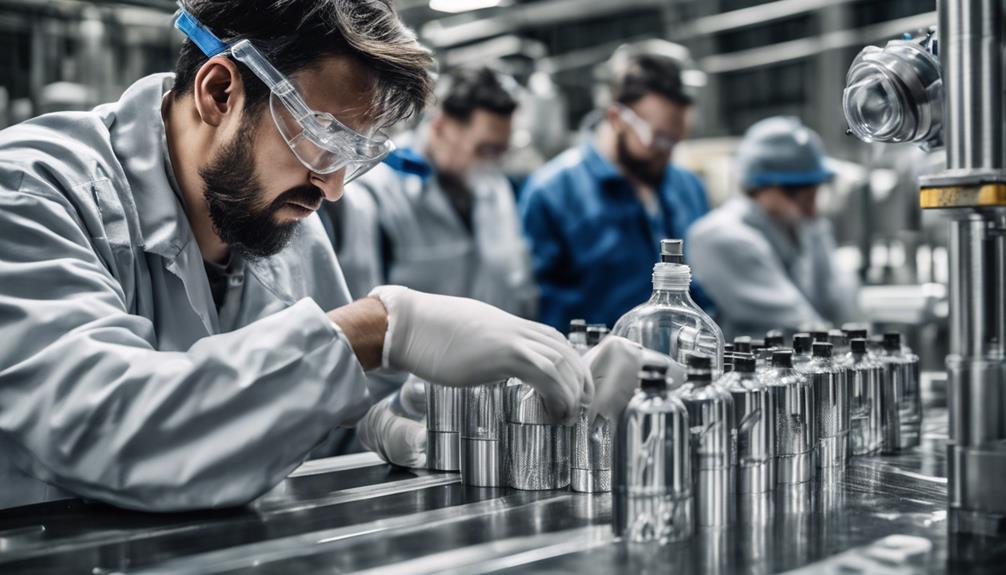
To ensure the highest quality standards in metal water bottle manufacturing, meticulous defect detection procedures are implemented throughout the production process. Quality assurance is paramount in meeting customer satisfaction.
Here are some key steps to ensure defect prevention and corrective action:
- Routine Inspections: Regular inspections at various stages of production help catch defects early on. This proactive approach minimizes the chances of defects passing through to the final product.
- Training Programs: Implementing thorough training programs for staff on defect detection techniques enhances the overall quality of the manufacturing process. Well-trained employees can identify and address issues promptly.
- Root Cause Analysis: Conducting root cause analysis on detected defects helps in understanding the underlying reasons. This analytical approach enables effective corrective actions to prevent similar defects in the future.
- Continuous Improvement: Establishing a culture of continuous improvement fosters a proactive mindset towards defect prevention. By constantly refining processes based on past experiences, the quality standards can be elevated, leading to increased customer satisfaction.
Compliance With Industry Standards
To ensure your metal water bottle manufacturing processes meet the highest standards, it's crucial to adhere strictly to industry guidelines.
Regular regulatory compliance checks should be conducted to guarantee that your production methods align with the latest industry regulations.
Implementing robust quality control processes will help you maintain consistency and excellence in your metal water bottle manufacturing operations.
Industry Standards Adherence
Ensure that your metal water bottle manufacturing process complies with industry standards to guarantee quality and safety. Adhering to industry standards is crucial for maintaining the integrity of your products and ensuring customer satisfaction. To achieve this, consider the following:
- Regular Auditing: Conduct routine audits of your manufacturing process to identify any deviations from industry standards promptly.
- Employee Training Programs: Implement ongoing training programs to enhance employee skills and knowledge, ensuring they're up to date with the latest industry standards and best practices.
- Quality Control Checks: Integrate quality control checkpoints throughout the manufacturing process to catch any non-compliance issues early on and rectify them swiftly.
- Supplier Compliance: Ensure that your suppliers also adhere to industry standards, as any deviation in their processes can affect the quality of your final product.
Regulatory Compliance Checks
Regular auditing of your manufacturing process is imperative to verify regulatory compliance with industry standards and uphold product quality and safety. Compliance audits, along with thorough product testing, are essential components of ensuring that your metal water bottles meet the required regulatory guidelines.
By conducting regular compliance audits, you can proactively identify any deviations from the established standards and take corrective actions promptly.
Product testing is another critical aspect of regulatory compliance checks. Through rigorous testing procedures, you can validate the quality and safety of your metal water bottles, ensuring that they meet the necessary regulatory guidelines.
This quality assurance process not only helps in adhering to industry standards but also enhances customer satisfaction by delivering a reliable and safe product.
Quality Control Processes
Implementing stringent quality control processes is essential to guarantee compliance with industry standards in metal water bottle manufacturing. By focusing on defect prevention and continuous process improvement, you can ensure that the final product meets the highest quality requirements.
Here are four key steps to enhance quality control and meet industry standards:
- Regular Quality Audits: Conduct frequent audits to identify any deviations from set quality standards and promptly address them. This proactive approach helps in maintaining consistency and adherence to industry requirements.
- Training Programs: Implement comprehensive training programs for employees involved in the manufacturing process. Well-trained staff are better equipped to spot potential issues, contributing to overall quality assurance.
- Root Cause Analysis: In case of quality issues, perform thorough root cause analysis to determine the underlying reasons. This step aids in implementing corrective actions and preventing similar defects in the future.
- Customer Feedback Integration: Incorporate customer feedback into the quality control process. Customer satisfaction is paramount, and by listening to their input, you can tailor your manufacturing processes to meet their expectations effectively.
Frequently Asked Questions
How Does Quality Control Impact the Overall Cost of Metal Water Bottle Manufacturing?
When assessing the impact of quality control on manufacturing costs, consider how stringent inspection processes can enhance product quality, leading to reduced defects and rework expenses. Emphasizing manufacturing quality ultimately influences overall cost.
What Measures Are Taken to Ensure Ethical Sourcing of Materials?
You might think ethical sourcing is as easy as a stroll in the park. Well, buckle up! Achieving supply chain transparency involves audits, certifications, and due diligence. Scrutinizing labor practices ensures fair treatment from start to finish.
Are There Any Specific Protocols for Monitoring the Production Environment?
To maintain high production standards, it's essential to implement rigorous environmental monitoring protocols. By closely overseeing the production environment, you can ensure that quality is maintained, waste is minimized, and sustainability goals are met.
How Is the Durability of Metal Water Bottles Tested Under Extreme Conditions?
When testing metal water bottles under extreme conditions, you'll see them endure harsh environments like champions in a fierce competition. Durability testing involves subjecting bottles to extreme heat, cold, pressure, impact, and corrosion simulations.
How Are Defects Addressed in the Manufacturing Process to Prevent Recalls?
To prevent defects in metal water bottle manufacturing, you conduct rigorous quality checks at every stage. By identifying issues early, you ensure recall prevention and deliver flawless products. Your attention to detail safeguards quality.
Conclusion
As you sip from your metal water bottle, remember the meticulous quality control measures that went into its manufacturing. From sourcing materials to testing for durability, every step ensures your safety and satisfaction.
Rest assured that industry standards have been met, defects have been corrected, and your bottle is built to last. So drink up, knowing that your trust in quality control has been well placed.