In the future of metal water bottle manufacturing, industry pioneers are embracing sustainable practices, advanced production techniques, smart technology integration, customization, durability enhancements, ethical sourcing, and streamlined processes. Recycled materials, robotic automation, data-driven production, personalization options, innovative coatings, and circular economy principles are shaping the landscape. The focus on operational efficiency, environmental impact, and consumer preferences drives innovation. Stay ahead in this dynamic industry by exploring these cutting-edge trends and market insights.
Key Takeaways
- Implement robotic automation and additive manufacturing for efficient production.
- Prioritize sustainable practices to reduce environmental impact and promote circular economy.
- Integrate smart technology for operational efficiency and innovation.
- Offer customization options for personalized products and increased customer satisfaction.
- Embrace ethical sourcing, cost-effectiveness, and lean practices for a competitive edge.
Sustainable Materials
To create eco-friendly metal water bottles, manufacturers frequently incorporate recycled materials into the production process. By utilizing recyclable materials, such as recycled stainless steel or aluminum, the manufacturing of metal water bottles becomes more sustainable and environmentally friendly. These eco-friendly designs not only reduce the demand for raw materials but also help in minimizing energy consumption during production.
Incorporating recycled materials into metal water bottle manufacturing not only benefits the environment but also contributes to a circular economy where resources are used efficiently and waste is minimized. By giving new life to materials that have already been used, manufacturers can reduce the environmental impact of their products and promote a more sustainable way of production.
Innovative approaches to sourcing and utilizing recyclable materials in the production of metal water bottles showcase the industry's commitment to sustainability. By focusing on eco-friendly design practices and incorporating recycled materials, manufacturers can create products that aren't only durable and functional but also contribute to a greener future.
Advanced Production Techniques

Implementing cutting-edge automation technologies enhances the efficiency and precision of metal water bottle manufacturing processes. Robotic automation and additive manufacturing play pivotal roles in revolutionizing how metal water bottles are produced.
Here are key advancements in production techniques:
- Robotic Automation: Introducing robotic arms into the manufacturing line streamlines tasks such as welding, polishing, and quality control, resulting in faster production cycles and improved consistency.
- Additive Manufacturing: Utilizing 3D printing techniques allows for intricate designs and customization options that were previously unattainable with traditional manufacturing methods.
- Automated Quality Inspection: Implementing automated systems for inspecting finished metal water bottles ensures that each product meets the highest quality standards before reaching the market.
- Data-Driven Production: Leveraging real-time data analytics to optimize production processes, minimize waste, and enhance overall operational efficiency.
Smart Technology Integration
Incorporating smart technology into metal water bottle manufacturing processes enhances operational efficiency and product quality through automated data analysis and real-time monitoring. By implementing data tracking systems, manufacturers can gather valuable insights into their production processes, identifying areas for optimization and improvement.
Automation plays a crucial role in streamlining operations, reducing manual labor, and minimizing the risk of errors.
Connectivity is a key aspect of smart technology integration in metal water bottle manufacturing. Through interconnected systems, data can be seamlessly shared between different stages of production, enabling a more coordinated and efficient workflow. This connectivity fosters innovation by allowing for the implementation of advanced technologies such as Internet of Things (IoT) devices and machine learning algorithms.
Customization and Personalization
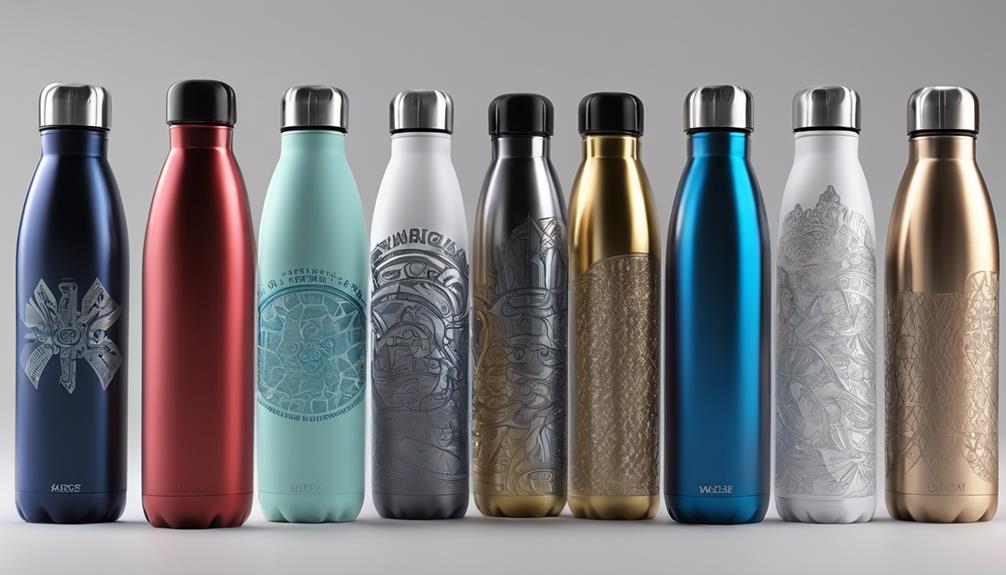
Enhancing metal water bottle manufacturing with customization and personalization capabilities enables manufacturers to meet diverse consumer demands and create unique, tailored products. Offering custom design and engraving options allows individuals to express their personal style and preferences on their water bottles.
Personalized color choices and patterns further enhance the individuality of each product, catering to specific tastes and needs. By integrating these customization features into the manufacturing process, companies can not only increase customer satisfaction but also foster brand loyalty and differentiation in the market.
Custom design and engraving options provide a platform for self-expression.
Personalized color choices and patterns allow for unique aesthetics.
Tailoring products to individual preferences enhances user experience.
Meeting diverse consumer demands through customization fosters brand loyalty.
Enhanced Durability and Performance
To improve durability and performance, manufacturers are incorporating tougher materials and advanced insulation technology in metal water bottles.
These enhancements not only increase the lifespan of the bottle but also ensure better temperature retention for your beverages.
Tougher Materials
For optimal durability and performance, metal water bottle manufacturing has increasingly focused on utilizing advanced materials resistant to wear and tear in harsh conditions. To ensure your metal water bottle can withstand the toughest adventures, manufacturers are incorporating cutting-edge technologies and materials.
- High Performance Alloys: By blending different metals, high-performance alloys are created to provide superior strength and corrosion resistance.
- Innovative Coatings: Special coatings are applied to metal water bottles to enhance scratch resistance and improve overall durability.
- Titanium Reinforcements: Incorporating titanium in key areas of the bottle increases its robustness without adding unnecessary weight.
- Impact-Resistant Designs: Bottles are now designed with reinforced bottoms and thicker walls to prevent damage from accidental drops or impacts.
These advancements in material science are revolutionizing the durability and performance of metal water bottles, ensuring they can keep up with your active lifestyle without compromising on quality.
Advanced Insulation Technology
Advanced insulation technology in metal water bottle manufacturing plays a crucial role in enhancing durability and performance for optimal usage in various conditions. By incorporating innovative design elements, these metal water bottles can now offer superior temperature control, keeping your beverages hot or cold for extended periods. The insulation technology not only prevents heat transfer but also ensures that the exterior of the bottle remains at a comfortable temperature to hold.
Temperature Control | Innovative Design | Durability | Performance |
---|---|---|---|
Ensures optimal temperature of beverages | Sleek and ergonomic designs | Resistant to dents and scratches | Maintains beverage freshness |
Minimizes heat transfer | Advanced sealing mechanisms | Long-lasting materials | Consistent insulation properties |
Keeps beverages hot/cold for hours | Customizable insulation layers | Impact-resistant construction | Enhanced pour control |
Streamlined Supply Chain Processes
You need to optimize your metal water bottle manufacturing process by implementing efficient sourcing strategies and lean production methods.
By streamlining your supply chain processes, you can reduce lead times, minimize waste, and enhance overall productivity.
This strategic approach ensures a cost-effective and agile production system that meets market demands efficiently.
Efficient Sourcing Strategies
Implementing just-in-time inventory management can significantly enhance the efficiency of sourcing strategies in the metal water bottle manufacturing process. By adopting this approach, you can reduce excess inventory, minimize storage costs, and improve responsiveness to changing market demands.
Furthermore, implementing automated reorder systems can help streamline the procurement process and ensure a consistent supply of raw materials for production.
Here are four key strategies to optimize your sourcing efficiency:
- Utilize Global Partnerships: Collaborating with suppliers from different regions can diversify your sourcing options and reduce the risk of supply chain disruptions.
- Focus on Eco-Friendly Initiatives: Prioritize suppliers that adhere to sustainable practices to align with consumer preferences and reduce environmental impact.
- Embrace Ethical Sourcing Practices: Ensure that your suppliers follow ethical labor standards and fair trade practices to uphold corporate social responsibility.
- Seek Cost-Effective Solutions: Evaluate different pricing models and negotiate favorable terms with suppliers to lower production costs without compromising quality.
Lean Production Methods
To enhance operational efficiency and minimize waste in metal water bottle manufacturing, employing lean production methods can streamline supply chain processes effectively. By integrating automation into manufacturing processes, tasks that were once time-consuming and prone to errors can be completed swiftly and accurately. Automation integration not only accelerates production but also reduces the chances of defects, enhancing overall product quality.
Waste reduction strategies play a crucial role in lean production methods, ensuring that resources are utilized optimally. Implementing practices like Just-In-Time manufacturing helps in minimizing excess inventory, lowering storage costs, and preventing overproduction.
Additionally, techniques such as value stream mapping can identify areas of improvement within the production process, leading to enhanced efficiency and reduced lead times.
Circular Economy Practices
Embracing circular economy practices in the manufacturing of metal water bottles involves rethinking traditional production methods and materials management. By incorporating recycled materials and implementing closed-loop systems, the industry can significantly reduce waste and environmental impact.
Here are four key strategies for implementing circular economy practices in metal water bottle manufacturing:
- Material Traceability: Utilize blockchain technology to track the journey of recycled materials used in bottle production, ensuring transparency and accountability.
- Design for Disassembly: Develop bottles that are easy to disassemble at the end of their life cycle, facilitating material separation for recycling.
- Reverse Logistics: Implement efficient systems for collecting used bottles from consumers, enabling proper recycling and reintroduction into the production process.
- Collaborative Partnerships: Form alliances with recycling facilities and material suppliers to create a closed-loop system that promotes sustainability and resource efficiency.
Market Trends and Consumer Preferences
Market trends and consumer preferences play a pivotal role in shaping the demand and direction of metal water bottle manufacturing processes. As the focus on sustainability intensifies, eco-friendly designs have become a significant trend in the market. Consumers are increasingly opting for metal water bottles that aren't only durable and convenient but also align with their eco-conscious values.
This shift towards sustainability has led manufacturers to prioritize the use of recyclable materials and energy-efficient production methods.
Changing consumer habits are also influencing the design and features of metal water bottles. With an emphasis on health and wellness, consumers are looking for bottles that are easy to clean, free from harmful chemicals, and capable of keeping beverages at the desired temperature for extended periods.
Additionally, customization options and stylish designs are becoming more sought after as consumers view their water bottles as not just a functional item, but also a fashion statement. By staying attuned to these market trends and consumer preferences, manufacturers can adapt their strategies to meet the evolving demands of the industry.
Frequently Asked Questions
How Does Metal Water Bottle Manufacturing Impact the Environment?
Metal water bottle manufacturing has a significant environmental impact due to resource extraction and energy use. To mitigate this, companies are implementing sustainability initiatives like recycling programs and using renewable energy sources for production.
Are There Any Health Concerns Associated With Using Metal Water Bottles?
Metal water bottle safety is a priority. Ensure bottles are BPA-free and clean regularly to prevent bacteria buildup. Consider alternatives like glass or silicone if concerned. Stay informed about potential health risks.
What Is the Average Lifespan of a Metal Water Bottle?
When considering metal water bottle durability, remember the benefits of reusable bottles. These vessels, like loyal companions, can last for years if cared for properly. Their average lifespan ranges from 5 to 10 years.
Can Metal Water Bottles Be Recycled at the End of Their Life?
Yes, metal water bottles can be recycled at the end of their life. Recycling possibilities offer a sustainable solution, mitigating the environmental impact by reducing waste and conserving resources. Proper recycling practices are essential for a greener future.
Are There Any Regulations or Standards for Metal Water Bottle Production?
To ensure regulations compliance in metal water bottle production, manufacturers must adhere to strict standards in their manufacturing processes. This guarantees product quality and sustainability, fostering innovation in the industry while meeting environmental responsibilities.
Conclusion
In conclusion, with the rise in demand for sustainable products, the metal water bottle manufacturing industry is poised for significant growth.
According to a recent study, the global market for metal water bottles is projected to reach $15 billion by 2025, highlighting the increasing importance of eco-friendly and durable alternatives to single-use plastics.
By embracing advanced production techniques, smart technology integration, and customization options, manufacturers can stay ahead of market trends and meet consumer preferences for sustainable and personalized products.