Crafted meticulously, stainless steel water bottles begin with high-grade alloys chosen for durability and corrosion resistance. Laser cutting techniques precisely shape the steel sheets, ensuring seamless fitting and intricate designs. Welding and polishing refine edges for a professional finish. Quality checks like hydrostatic and air pressure testing guarantee leak-proof functionality. With a focus on aesthetics and sustainability, these bottles offer personalized engravings and color options. The intricate process ensures every bottle meets strict quality standards, from precision shaping to final packaging. Each step contributes to creating a durable, eco-conscious, and stylish stainless steel water bottle.
Key Takeaways
- Utilize high-grade stainless steel alloys for durability and corrosion resistance.
- Employ laser cutting for precise shaping and intricate designs.
- Implement hydroforming for cost-effective production of complex bottle shapes.
- Ensure final finishing with polish, protective coating, and custom engravings.
- Conduct rigorous testing for leak-proof functionality and quality assurance.
Raw Materials Selection
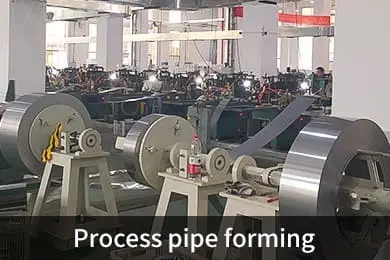
When selecting raw materials for stainless steel water bottles, prioritize high-grade stainless steel alloys to ensure durability and resistance to corrosion. Material sourcing plays a crucial role in ensuring the quality and longevity of the final product. Opt for sustainable sourcing practices to minimize environmental impact and promote ethical standards throughout the supply chain.
Manufacturing efficiency is key in the production of stainless steel water bottles. By using high-grade stainless steel alloys, you can streamline the manufacturing process and reduce the need for additional treatments or coatings. This not only saves time but also contributes to cost-saving measures by cutting down on extra manufacturing steps.
Choosing the right stainless steel alloys is essential for creating durable and long-lasting water bottles. By focusing on quality materials, you can ensure that the final product meets high standards of strength and corrosion resistance. Prioritizing sustainability in material selection benefits both the environment and the overall quality of the stainless steel water bottles.
Stainless Steel Cutting Process
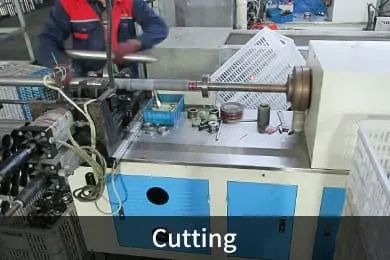
When shaping stainless steel water bottles, the cutting process begins with steel sheet preparation to ensure a clean surface.
Laser cutting techniques are then employed for precise and intricate designs, creating sharp edges with high accuracy for a polished finish.
This process guarantees that the stainless steel pieces fit together seamlessly, forming durable and sleek water bottles.
Steel Sheet Preparation
To prepare stainless steel sheets for water bottle production, the steel cutting process involves precise cutting techniques to ensure accurate dimensions and clean edges. Stainless steel, known for its exceptional material strength, undergoes a meticulous shaping process before being transformed into water bottle components.
Here is an overview of the steel sheet preparation steps:
- Material Selection: High-quality stainless steel sheets are carefully chosen based on the required specifications for the water bottle design.
- Measurement and Marking: Accurate measurements are taken, and precise markings are made on the steel sheets to guide the cutting process.
- Cutting Method Selection: Depending on the thickness and type of stainless steel, suitable cutting methods such as shearing or sawing are selected.
- Deburring: After cutting, any rough edges or burrs are removed to ensure a smooth and safe finish for the water bottle production process.
Laser Cutting Technique
For precision cutting of stainless steel sheets in water bottle production, the laser cutting technique offers unparalleled accuracy and efficiency in shaping the material. Laser cutting utilizes a high-powered laser beam focused on the stainless steel sheet, melting or vaporizing the material along the desired cutting path. This results in clean, precise cuts that are crucial for creating the intricate designs required for custom water bottle production.
In addition to cutting, laser engraving is commonly used to add branding options and custom designs to stainless steel water bottles. The laser engraving process uses the same high-precision laser beam to etch permanent markings onto the surface of the bottle, ensuring durability and a professional finish.
Before proceeding with production, durability testing is often conducted on the laser-cut stainless steel sheets to ensure they meet the rigorous standards required for water bottle manufacturing. This testing helps guarantee that the bottles can withstand daily use and washing without compromising the integrity of the material.
Precision Edges Formation
Utilizing advanced laser cutting technology, the precision edges formation process in stainless steel cutting involves the accurate shaping of the material to achieve intricate designs for water bottle production. This crucial step ensures that the stainless steel water bottles have smooth, precise edges that not only enhance the aesthetic appeal but also contribute to the overall durability and functionality of the final product.
The precision edges formation process encompasses various intricate techniques to achieve the desired results, including edge polishing techniques and precision welding processes.
- Laser cutting technology precisely shapes stainless steel sheets.
- Edge polishing techniques refine the edges for a smooth finish.
- Precision welding processes join the edges seamlessly to form the bottle.
- Advanced machinery ensures accuracy in edge formation for consistent quality.
Forming the Bottle Shape

When shaping stainless steel water bottles, a process known as hydroforming is commonly utilized to achieve the desired form. Hydroforming is a metal forming technique that uses high-pressure fluid to shape the metal into the desired mold. This process allows for complex shapes to be formed with precision and efficiency. The stainless steel sheet is placed into a mold, and high-pressure water is then pumped into the sheet, causing it to take on the shape of the mold through hydraulic pressure.
Benefits of Hydroforming | Description |
---|---|
Complex Shapes | Hydroforming allows for the production of intricate bottle shapes. |
Uniform Wall Thickness | The process ensures consistent wall thickness throughout the bottle. |
Efficient Production | Hydroforming is a cost-effective method for shaping stainless steel bottles. |
Hydroforming is favored in the manufacturing of stainless steel water bottles due to its ability to create seamless and durable designs. This shaping technique results in bottles that are not only visually appealing but also highly functional.
Welding the Seams
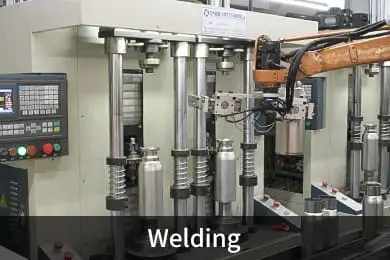
When welding the seams of stainless steel water bottles, precision is paramount.
Ensuring a seamless bond strength is crucial for the durability and leak-proof nature of the bottle.
Precision seam welding techniques are utilized to achieve a seamless bond strength that guarantees the integrity of the bottle.
Precision Seam Welding
Precision seam welding is a critical process in manufacturing stainless steel water bottles. It involves meticulously joining the seams with high accuracy and consistency to ensure the overall durability and strength of the bottle.
Here are some key aspects of precision seam welding:
- Welding Techniques: Various welding techniques are utilized, such as TIG (Tungsten Inert Gas) welding or laser welding, to create precise and strong seams that can withstand the rigors of everyday use.
- Seam Strength: The focus is on achieving optimal seam strength through meticulous control of welding parameters, ensuring that the seams are secure and leak-proof.
- Precision Welding: Every weld is executed with precision to maintain the structural integrity of the bottle, preventing any weak points that could compromise its durability.
- Bottle Durability: The quality of the seam welding directly impacts the overall durability of the stainless steel water bottle, making it resistant to dents, corrosion, and other damage.
Seamless Bond Strength
To ensure the seamless bond strength of stainless steel water bottles, the welding of the seams is meticulously conducted with precision and attention to detail. Bonding techniques play a crucial role in creating a durable and leak-proof container. Manufacturers utilize various methods such as laser welding, TIG welding, or resistance welding to join the stainless steel sheets seamlessly. These techniques ensure that the seams are fused together securely, preventing any potential weak points that could compromise the bottle's integrity.
After the welding process, rigorous strength testing is performed to verify the quality of the bond. This testing involves subjecting the welded seams to extreme pressures to assess their resistance to leakage or separation. Any bottles that don't meet the specified strength requirements are rejected to maintain the highest standards of quality control.
Annealing for Strength
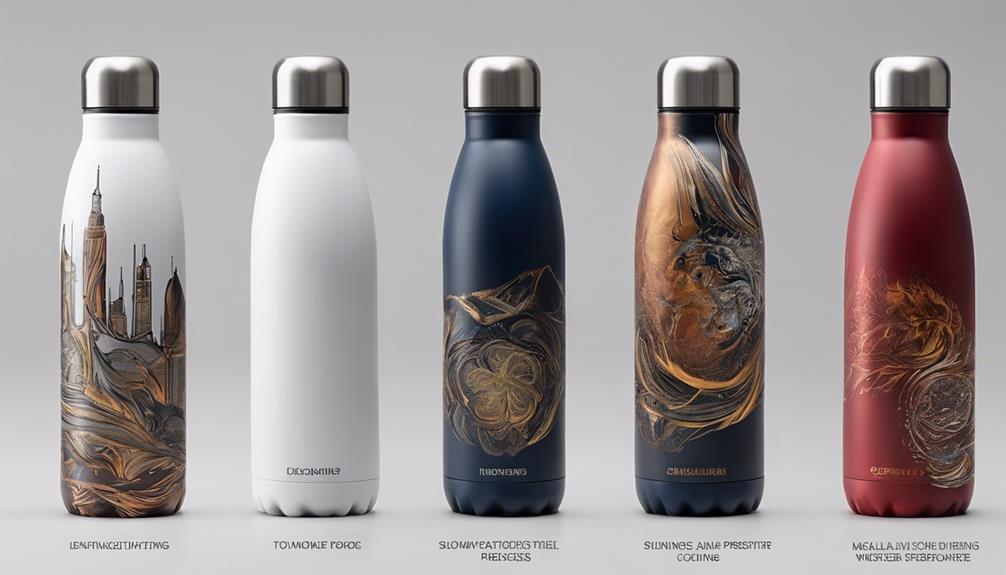
Annealing stainless steel water bottles is a crucial process in enhancing their strength and durability. During annealing, the bottles are heated to specific temperatures and then slowly cooled down to alter their microstructure and remove internal stresses, ultimately improving their mechanical properties.
Precise temperature control is essential during annealing to achieve the desired metallurgical changes without compromising the material's integrity.
The cooling process after heating is carefully managed to ensure a controlled transformation of the steel's structure, enhancing its strength.
Annealing allows for the adjustment of the steel's microstructure, leading to improved hardness and toughness.
Through annealing, internal stresses accumulated during manufacturing processes are mitigated, preventing potential weaknesses in the final product.
Surface Treatment and Cleaning
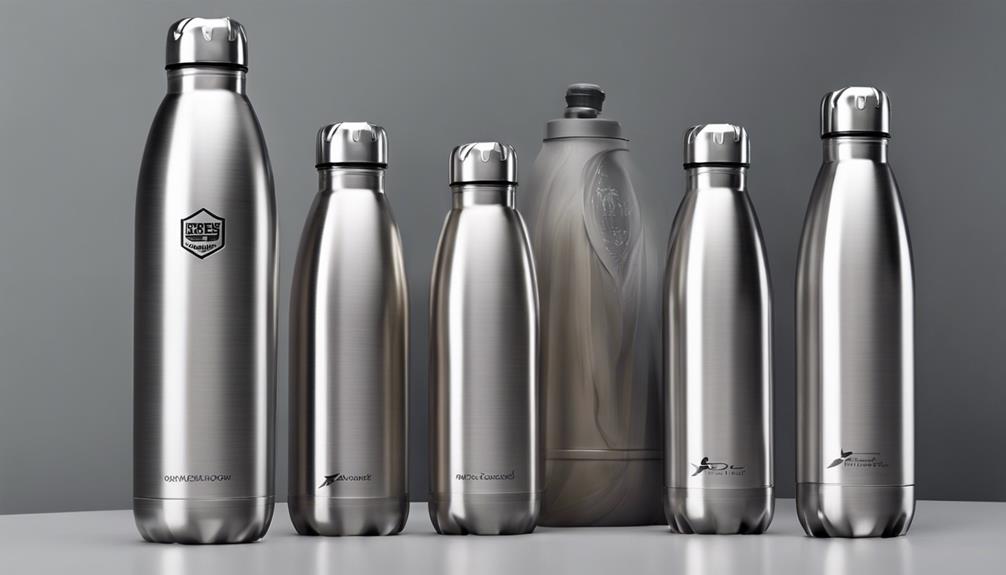
When cleaning stainless steel water bottles, it's crucial to follow a meticulous process to ensure the surface remains pristine and safe for use.
Surface treatment plays a vital role in maintaining the integrity and longevity of the bottle, safeguarding it against corrosion and other potential damages.
Cleaning Process Overview
Effective maintenance of stainless steel water bottles requires a systematic approach to surface treatment and cleaning. To ensure the longevity and hygiene of your bottle, follow these key steps:
- Eco-Friendly Cleaning: Use a mixture of warm water and mild dish soap to clean the bottle thoroughly. Avoid harsh chemicals that can damage the stainless steel surface.
- Sanitizing Techniques: Periodically sanitize your water bottle by using a solution of water and white vinegar or baking soda. Let the solution sit for a few hours before rinsing it out.
- Sustainable Packaging: When storing your stainless steel water bottle, opt for sustainable packaging such as cloth bags or reusable cases to protect it from scratches or dents.
- Safe Storage Options: Store your bottle in a cool, dry place away from direct sunlight to prevent discoloration and maintain the quality of the stainless steel material.
Importance of Surface Treatment
Surface treatment plays a crucial role in maintaining the quality and longevity of stainless steel water bottles. Chemical treatments are applied to the surface of stainless steel bottles to enhance their resistance to corrosion and rust. These treatments often involve passivation processes that create a protective layer on the metal surface, preventing the formation of rust and increasing the overall durability of the bottle.
Rust prevention is a key aspect of surface treatment for stainless steel water bottles. By utilizing specialized coatings or finishes, manufacturers can significantly reduce the risk of rust formation, even when the bottles are exposed to moisture or harsh environmental conditions. These coatings act as a barrier, preventing water and oxygen from reaching the metal surface and initiating the corrosion process.
Adding Special Features
Consider incorporating innovative features like a built-in filtration system or a leak-proof design to enhance the functionality of stainless steel water bottles. These special features can elevate the user experience and set your product apart from the competition.
Here are some advanced features to consider:
- Custom Engraving: Personalize each bottle with a unique design or name, adding a touch of individuality.
- Temperature Control: Implement a double-wall vacuum insulation system to keep beverages hot or cold for extended periods.
- Integrated Straw: Incorporate a retractable or foldable straw for convenient sipping on the go.
- Safety Lock Mechanism: Develop a secure locking mechanism to prevent accidental spills and ensure peace of mind during transport.
Quality Inspection Procedures
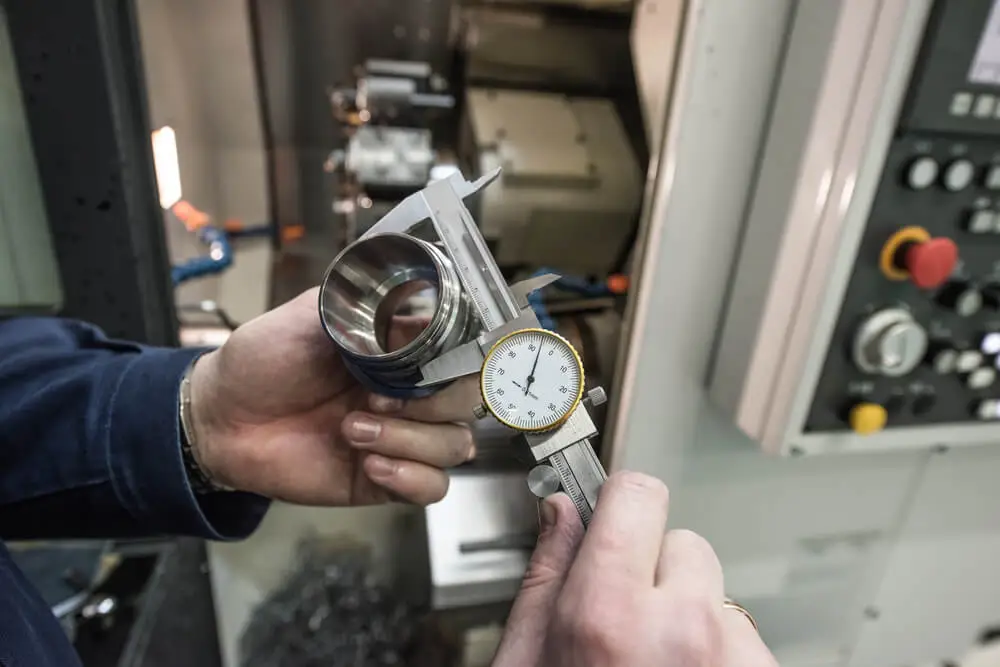
You'll learn about the visual inspection process used to ensure the quality of stainless steel water bottles.
Discover the leak testing methods employed to guarantee the bottles are leak-proof.
Explore the material composition analysis techniques that are utilized to verify the stainless steel's quality and safety standards.
Visual Inspection Process
Perform a detailed examination of the stainless steel water bottles using a standardized visual inspection process to ensure quality standards are met. Visual inspection techniques and quality control standards play a crucial role in this phase.
Here is a breakdown of the visual inspection process:
- Surface Finish Evaluation: Check for any scratches, dents, or discoloration that may affect the aesthetics of the bottle.
- Seam Inspection: Verify the integrity of the seams to prevent leakage or structural weaknesses.
- Label Alignment: Ensure that logos, text, and any other printed elements are correctly aligned and applied without defects.
- Cap and Lid Examination: Inspect the caps and lids for proper fit, alignment, and any defects that may hinder functionality.
Defect detection methods and inspection criteria are meticulously applied during this visual inspection to guarantee that each stainless steel water bottle meets the quality standards set forth. This detailed process helps maintain the overall integrity and functionality of the product.
Leak Testing Methods
To ensure the quality and reliability of stainless steel water bottles, leak testing methods are implemented as part of the quality inspection procedures. Leak prevention techniques and quality control measures play a crucial role in ensuring that the water bottles are free from any defects that could compromise their functionality. These methods help in identifying any potential leaks or weak points in the bottle's construction, ensuring that only high-quality products reach the market.
In line with sustainability efforts and to minimize the environmental impact, manufacturers often use non-destructive leak testing methods such as pressure decay testing, vacuum decay testing, or helium leak testing. These methods allow for thorough testing without damaging the product, aligning with eco-friendly practices.
The following table provides a comparison of different leak testing methods used in the production of stainless steel water bottles:
Leak Testing Method | Description | Advantages |
---|---|---|
Final Finish Process | Details | Benefits |
Final Polish | Achieves glossy finish | Enhanced aesthetics |
Protective Coating | Increases durability | Resistant to scratches |
Custom Engravings | Personalized touch | Unique and individualized |
Color Options | Variety of choices | Personalized appearance |
Pressure Testing for Leaks
Performing pressure tests is crucial to ensure the stainless steel water bottles meet quality standards and are free from leaks. Leak prevention techniques and quality control measures are implemented during this stage to guarantee a reliable final product.
Hydrostatic Testing: Bottles are filled with water and pressurized to check for leaks under water pressure.
Air Pressure Testing: Bottles are pressurized with air to identify any leaks by observing bubble formations.
Visual Inspection: Each bottle is meticulously examined for any imperfections or irregularities that may lead to leaks.
Drop Testing: Bottles are dropped from various heights to simulate real-life conditions and ensure the structural integrity of the bottle.
Attaching the Lid and Seal
During the assembly process, the lid is securely attached to the stainless steel water bottle, ensuring a tight seal for leak-proof functionality. The lid design is crucial in maintaining the overall aesthetics and functionality of the bottle. The seal quality is equally important to prevent any leakage of liquids.
The lid attachment process involves precise machinery that carefully aligns the lid with the bottle opening. Typically, the lid is threaded onto the bottle, creating a secure closure. This threaded design not only ensures a tight seal but also allows for easy opening and closing of the bottle.
The seal process is where the magic happens. A food-grade silicone or rubber gasket is placed between the lid and the bottle's opening. This gasket forms a watertight seal when the lid is securely attached. The quality of this seal is tested rigorously to guarantee leak-proof functionality, providing users with peace of mind when using the stainless steel water bottle.
Packing and Labeling
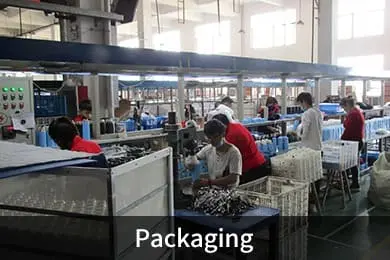
The packing process for stainless steel water bottles involves carefully placing the bottle in its designated packaging while ensuring all necessary labeling information is correctly affixed. When considering brand customization and marketing strategy, it's vital to create packaging that reflects the brand identity and appeals to the target market.
Here are four key aspects to consider during the packing and labeling phase:
- Consumer Preferences: Packaging should align with consumer preferences, such as eco-friendly materials or convenient designs that enhance usability.
- Design Trends: Staying updated with design trends ensures the packaging remains visually appealing and competitive in the market.
- Brand Customization: Incorporating brand elements like logos, colors, and taglines on the packaging helps reinforce brand recognition.
- Marketing Strategy: Utilize the packaging as a tool for marketing by including QR codes, product benefits, or testimonials to engage customers further.
Shipping to Distributors
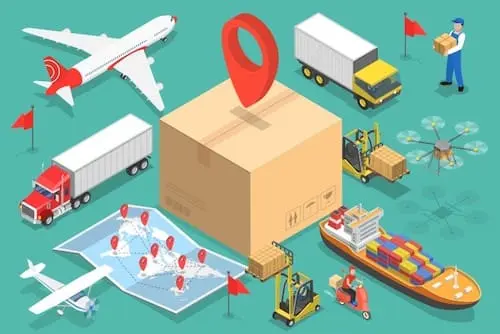
Shipping stainless steel water bottles to distributors requires efficient logistics management to ensure timely delivery and product integrity. Distributor partnerships play a crucial role in this process, as strong relationships facilitate smooth coordination and communication.
Global shipping trends impact the transportation of these bottles, influencing decisions on shipping routes, modes of transportation, and delivery timelines.
When shipping to distributors, it's essential to consider various factors such as distance, shipping costs, customs regulations, and delivery schedules. Utilizing advanced tracking technologies can help monitor shipments in real-time, providing visibility and control over the entire shipping process.
To optimize shipping operations, manufacturers often collaborate with logistics experts to streamline processes, minimize delays, and reduce shipping costs. By staying informed about global shipping trends, companies can adapt their strategies to meet changing market demands and ensure efficient distribution to their network of distributors worldwide.
Effective shipping practices are vital to maintaining a competitive edge in the stainless steel water bottle industry.
Maintaining and Caring for Your Bottle
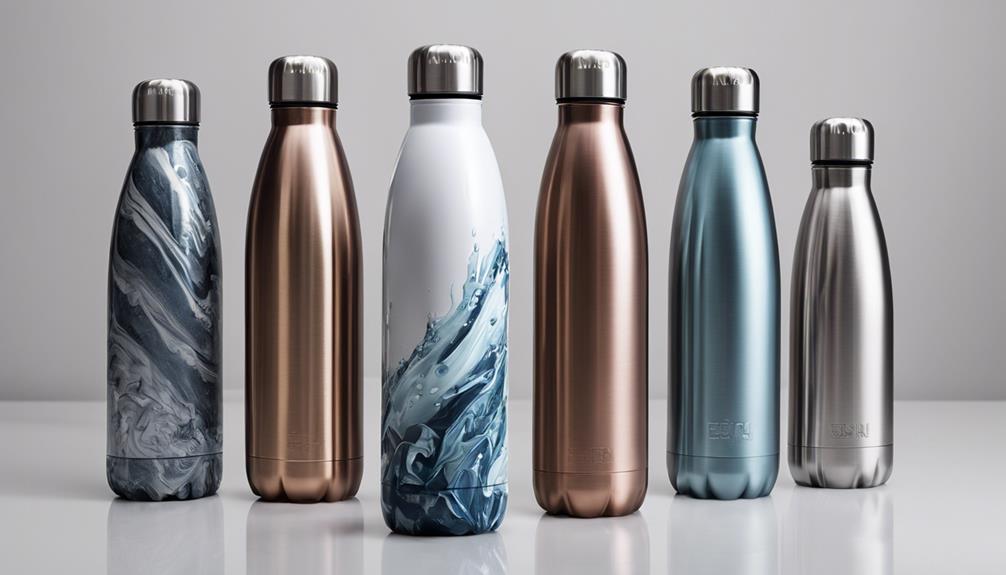
Proper maintenance and care of your stainless steel water bottle will ensure its longevity and optimal performance. To maintain your bottle effectively, wash it regularly with warm soapy water and rinse it thoroughly to prevent any residue buildup. Avoid using harsh chemicals, abrasive sponges, or bleach as they can damage the bottle's finish. Additionally, consider using a bottle brush to clean hard-to-reach areas inside the bottle.
When not in use, store your stainless steel water bottle with the lid off to allow for air circulation and prevent any lingering odors. Keep it away from extreme temperatures and don't freeze the bottle when it's full, as this can cause damage to the stainless steel material. If your bottle develops any dents or scratches, consider using a stainless steel polish to restore its appearance.
Following these caring tips won't only maintain the aesthetic appeal of your bottle but also prolong its lifespan, ensuring that you can enjoy the benefits of using a high-quality stainless steel water bottle for years to come.
Frequently Asked Questions
How Do Stainless Steel Water Bottles Compare to Plastic in Terms of Environmental Impact?
When comparing stainless steel water bottles to plastic in terms of environmental impact, consider recycling options and long term durability. Stainless steel bottles are more eco-friendly, as they are recyclable and have greater longevity.
Can Stainless Steel Water Bottles Affect the Taste of the Water?
When it comes to water purity, stainless steel water bottles can affect the taste due to the manufacturing process. However, proper cleaning and maintenance can minimize any impact, ensuring your water stays fresh and untainted.
Are There Any Health Concerns Associated With Using Stainless Steel Water Bottles?
When using stainless steel water bottles, consider potential health concerns. Stainless steel is generally safe but make sure it's BPA-free. Stay hydrated with confidence knowing your bottle safeguards your water's purity.
Can Stainless Steel Water Bottles Keep Beverages Hot or Cold for Extended Periods?
Sure! Stainless steel water bottles can keep beverages hot or cold for extended periods due to their excellent insulation effectiveness. Additionally, their material durability ensures they maintain temperature for hours, making them ideal for outdoor activities.
How Can I Safely Dispose of a Stainless Steel Water Bottle at the End of Its Life Cycle?
When disposing of a stainless steel water bottle, consider recycling options. Look for eco-friendly alternatives like metal recycling facilities or local recycling programs. Ensure the bottle is clean and separated from other materials for proper disposal.
Conclusion
Now that you know how stainless steel water bottles are made, you can appreciate the precision and craftsmanship that goes into each bottle.
From raw material selection to welding seams, every step is carefully executed to ensure a durable and eco-friendly product.
Remember to maintain and care for your bottle to keep it looking and functioning like new.
Embrace sustainability with a high-quality stainless steel water bottle that will last a lifetime.