If you're in the business of distributing stainless steel water bottles, then you know how important it is to have a sound logistics strategy. From managing inventory and choosing the right shipping method to packaging and labeling, every step in the distribution process can impact your bottom line.
But with so many factors to consider, it can be challenging to know where to start. In this article, we'll walk you through the key components of optimizing your logistics for stainless steel water bottle distribution.
We'll cover everything from understanding your customer base and managing inventory to implementing technology solutions and evaluating performance metrics. By following these best practices and continuously improving your processes, you can streamline your operations, reduce costs, and ultimately deliver a better product to your customers.
Understanding Your Customer Base
You gotta get inside the heads of your customers and really feel what they want in their reusable water bottles. Customer segmentation is essential to understanding the different demographics that are interested in purchasing a stainless steel water bottle.
This process involves dividing your market into smaller groups based on characteristics such as age, gender, income level, and lifestyle. Once you have identified these groups, it's important to conduct market research to gather more information about their specific needs and preferences.
This can involve surveys, focus groups, or even just observing customer behavior in stores or online. By gathering this data, you can gain valuable insights into which features are most important to each group of customers. For example, some customers may prioritize durability and insulation capabilities over design aesthetics.
Others may be looking for a compact size that fits easily in a backpack or purse. Understanding these nuances allows you to tailor your product offerings and marketing messages accordingly, ultimately leading to more satisfied customers and increased sales.
So before diving headfirst into logistics optimization for distribution of stainless steel water bottles, take the time to truly understand your customer base through proper segmentation and research techniques.
Inventory Management
To optimize your inventory management for stainless steel water bottle distribution, you'll need to implement a tracking system that allows you to monitor stock levels and sales data in real time. Setting reorder points will ensure you never run out of popular products, while minimizing excess inventory that ties up capital.
Managing stock levels effectively will help you reduce costs by avoiding overstocking and eliminating dead stock. By implementing these key practices, you can improve efficiency and profitability in your distribution operations.
Implementing a tracking system
By implementing a tracking system, the logistics of distributing stainless steel water bottles can be optimized. Two key factors that can help achieve this goal are real-time tracking implementation and GPS-enabled logistics optimization.
With real-time tracking implementation, you can easily monitor every aspect of your supply chain in real-time. You'll be able to locate your inventory quickly and efficiently, making it easier to manage stock levels and prevent stockouts. This will also allow you to optimize delivery routes and schedules, reducing transportation costs while ensuring timely delivery.
A GPS-enabled logistics optimization solution allows you to track your shipments more accurately and efficiently. By using GPS technology, you can determine the most efficient route for each shipment, taking into account traffic conditions and other variables that may impact delivery times. This helps you reduce transportation costs while improving customer satisfaction by ensuring that products are delivered on time.
With these tools in place, you'll be able to streamline your operations and deliver a better experience for customers while maximizing efficiency and profitability.
Setting reorder points
When setting reorder points, it's important to consider the demand for your product and how quickly you can receive new inventory. Reorder point calculation is a critical aspect of inventory optimization, as it ensures that you always have adequate stock levels to meet customer demand without overstocking which could lead to additional costs such as storage or spoilage.
To determine the optimal reorder point, you need to consider factors such as lead time (time taken from placing an order until receiving it), safety stock (additional inventory held in case of unexpected demand or delayed deliveries), and order frequency (how often you place orders). By analyzing these factors, you can establish an efficient system that balances supply and demand while minimizing unnecessary expenses.
Factor | Formula | Example |
---|---|---|
Lead Time | Average time taken from placing an order until receiving it | 5 days |
Safety Stock | Desired level of additional inventory held in case of unexpected demand or delayed deliveries | 50 units |
Order Frequency | How often you place orders based on sales volume and supplier availability | Once a week |
By taking into account these factors, businesses can set effective reorder points that ensure adequate supply levels while reducing excess inventory. This not only optimizes logistics operations but also helps increase profitability by minimizing storage costs and improving cash flow management.
Managing stock levels
Maintaining proper stock levels is crucial for businesses to meet customer demand and prevent lost sales. To do this effectively, you need a solid understanding of your supplier management process and demand forecasting.
By keeping track of your suppliers' lead times, delivery schedules, and pricing fluctuations, you can ensure that you always have enough inventory on hand without overstocking or overspending. Demand forecasting involves analyzing historical sales data, market trends, and seasonality patterns to predict future demand for your products. This allows you to anticipate sales spikes and adjust your stock levels accordingly.
It's important to regularly review and update your inventory levels based on changes in customer preferences or purchasing habits. By staying on top of these factors and implementing effective supply chain management practices, you can optimize logistics for the distribution of stainless steel water bottles and ensure that your business runs smoothly.
Choosing the Right Shipping Method
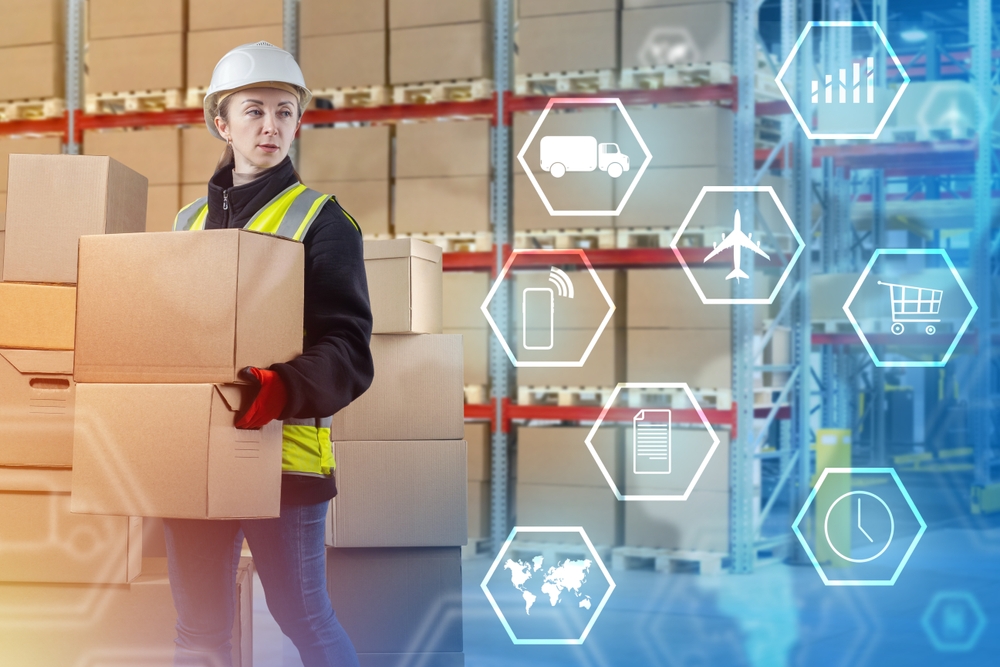
To find the most efficient way to distribute your stainless steel water bottles, you should consider which shipping method will work best for your business needs. There are different options available, such as air freight, sea freight, and ground transportation.
Each of these methods has its advantages and disadvantages that you need to weigh in before making a decision. Comparing costs is one of the essential factors when choosing the right shipping method. Air freight is usually faster but more expensive than sea or ground transportation. It may be suitable for small or urgent orders but could become too costly for larger shipments.
On the other hand, sea freight is more affordable but takes longer to arrive at its destination. Ground transportation may be more cost-effective and faster for shorter distances, but it's not ideal if you need to ship products across countries or continents. Another consideration when choosing a shipping method is fragility.
Stainless steel water bottles are durable items that can withstand some level of impact during transit. However, they still require proper handling and packaging to prevent damage during transport. When selecting a shipment option, make sure to choose one that provides adequate protection from potential shocks or vibrations that could affect your product's integrity upon arrival at its destination.
Packaging and Labeling
When it comes to packaging and labeling your stainless steel water bottles, you need to make sure that you choose appropriate packaging that protects the bottles during shipping.
It's also important to create clear labeling that helps customers understand what they're buying, how to use the product, and any special care instructions.
By taking the time to carefully package and label your products, you can improve customer satisfaction and reduce returns or complaints.
Choosing appropriate packaging
You'll want to pick packaging that keeps your stainless steel water bottles safe during transportation and makes a great first impression on your customers. The right packaging not only protects the product, but also helps to build trust with your buyers. When choosing packaging for your stainless steel water bottles, consider factors such as durability, environmental impact, and cost effectiveness.
To help you make an informed decision, here's a table outlining common types of packaging materials along with their pros and cons:
Packaging Material | Pros | Cons |
---|---|---|
Plastic wrap/bags | Inexpensive; protects from scratches and minor scuffs | Not environmentally friendly; prone to tearing/damage |
Bubble wrap | Provides extra cushioning; reusable if in good condition | Not eco-friendly; takes up more space than other materials |
Foam inserts/padding | Offers superior protection against damage; recyclable in some cases | More expensive than other options; not biodegradable |
Keep in mind that there are often trade-offs between cost, environmental impact, and protection levels when selecting packaging materials. It's important to weigh these factors carefully before making a final decision. Ultimately, the right choice will depend on your priorities as a business owner.
Creating clear labeling and instructions
Make sure your customers can easily understand how to use and care for their new reusable bottle with clear labeling and easy-to-follow instructions. The importance of clarity in labeling and instructions cannot be overstated, as it directly impacts customer satisfaction. Confusing or inadequate information can lead to frustration and dissatisfaction with the product, potentially damaging the brand's reputation.
Furthermore, customer engagement through feedback and suggestions can greatly improve the effectiveness of labeling and instructions. By listening to customer feedback, companies can identify areas where confusion or misunderstanding may occur and make necessary adjustments. This not only improves the user experience but also shows a commitment to continuously improving product quality.
Clear labeling and instructions combined with open communication between company and consumer create a positive relationship that leads to increased loyalty and repeat business.
Managing Returns and Exchanges
Handling returns and exchanges can be a complex process, but it's essential for ensuring customer satisfaction with their stainless steel water bottle purchase. Managing customer satisfaction is crucial in minimizing return rates.
To streamline this process, start by creating a clear and concise return policy that outlines the steps customers need to take when returning or exchanging their product.
When a customer initiates a return or exchange, respond promptly and professionally. Make sure to provide detailed instructions on how to proceed with the process and offer assistance if needed. If the issue is related to product quality or defects, take responsibility and offer options such as replacements or refunds.
It's also important to track returns and exchanges data carefully to identify patterns and improve overall customer experience. Use this information to analyze common issues that customers face when making returns or exchanges and make necessary changes in packaging, labeling, or instructions.
By managing returns and exchanges efficiently, you can reduce costs associated with lost sales while enhancing your reputation for providing excellent customer service.
Streamlining Order Fulfillment
To efficiently fulfill orders, it's important to have a well-organized system in place that seamlessly coordinates the packaging and shipment of your stainless steel water bottles. Maximizing efficiency and reducing costs are key goals for any business, and automating order processing can help achieve both. Here are some tips to streamline your order fulfillment process:
- Implement an Order Management System (OMS): An effective way to automate order processing is by using an OMS. This software can help you manage inventory levels, track orders, and generate shipping labels - all from one platform. By centralizing these tasks, you can reduce errors and save time on manual processes.
Benefits of an OMS:
- Improved accuracy in tracking orders
- Faster shipping times
- Increased visibility into inventory levels
- Optimize Your Warehouse Layout: A well-planned warehouse layout can also improve order fulfillment efficiency. Consider placing frequently ordered items closer to the packing area to minimize picking time. You may also want to invest in conveyor systems or other automation technologies that reduce labor costs and increase throughput.
Tips for Optimizing Your Warehouse:
- Use vertical space effectively with tall shelves or mezzanines
- Group similar products together for easy access
- Utilize technology such as barcode scanners or RFID tags
- Offer Multiple Shipping Options: Finally, offering multiple shipping options can improve customer satisfaction while reducing transportation costs. For example, customers who live near your distribution center could choose free local pickup instead of paying for shipping. Additionally, negotiating lower rates with carriers based on volume or transit time can save money in the long run.
Types of Shipping Options:
- Standard Ground Shipping
- Expedited Shipping
- Local Pickup
Improving Warehouse Management
You can maximize the efficiency of your warehouse by implementing new technologies and reorganizing the layout. One effective way to improve warehouse management is by integrating automation solutions. Automated systems can help increase productivity, reduce errors, and minimize labor costs. For instance, you can use automated storage and retrieval systems (AS/RS) to optimize inventory management and speed up order processing.
Another important aspect of improving warehouse management is workforce training. Your staff must be trained on how to properly operate the new technologies you've introduced in your facility. Training should also cover safety protocols and procedures for handling materials and equipment within the warehouse environment. By investing in proper training programs, you can ensure that your employees are equipped with the necessary skills to perform their tasks efficiently.
Reorganizing your warehouse layout can also contribute significantly to optimizing logistics for stainless steel water bottle distribution. You may want to consider designing a more efficient floor plan that maximizes space utilization while ensuring easy access to high-demand products. You could even implement lean principles such as 5S methodology or just-in-time (JIT) inventory management techniques to streamline processes further.
With these strategies in place, you'll be able to achieve faster turnaround times, reduce lead times for shipping orders, and ultimately enhance customer satisfaction levels through timely delivery of products.
Optimizing Transportation Routes
To optimize your transportation routes for distributing stainless steel water bottles, you need to analyze your current shipping routes and identify areas for improvement.
This will involve analyzing the time, cost, and efficiency of each route to determine which ones are most effective.
By identifying areas that need improvement, you can make adjustments to streamline your logistics process and ultimately save time and money.
Analyzing shipping routes
Visualize the most efficient shipping routes for your stainless steel water bottles by analyzing transportation data. This can help you identify which routes are most frequently used, which ones have the shortest distance and travel time, and which ones have the least amount of traffic or other obstacles.
By doing so, you can implement route optimization strategies that'll not only save you time and money but also ensure that your products reach their destination on time and in good condition. To achieve cost-effective transportation solutions, it's important to consider different factors such as fuel costs, labor costs, maintenance expenses, and other associated expenses.
Analyzing shipping routes can give you a better understanding of these factors and allow you to make informed decisions about how to optimize your logistics operations. With this information in hand, you can choose the best possible shipping routes for your business needs while minimizing any negative impact on the environment or local communities.
Ultimately, optimizing your logistics operations through route analysis can help increase efficiency and profitability while reducing waste and environmental impact.
Identifying areas for improvement
Take a moment to assess where your shipping operations can improve by identifying any bottlenecks or inefficiencies. Logistics challenges are inevitable when distributing stainless steel water bottles, especially when dealing with multiple suppliers and retailers across different regions. These challenges can lead to delays in delivery, higher costs, and dissatisfied customers.
To achieve operational efficiency, it's important to identify areas for improvement. This includes optimizing inventory management, streamlining shipping routes, and reducing transit time. Utilizing technology like GPS tracking and automated inventory systems can help streamline the distribution process while minimizing errors and increasing accuracy.
By implementing these improvements, you can reduce logistics challenges and create a more efficient supply chain that benefits both your business and your customers.
Communication and Coordination
To optimize your transportation routes for distributing stainless steel water bottles, you must establish clear communication channels with your shipping partners. This will help ensure that everyone is on the same page and that potential issues are addressed promptly.
Coordination with your shipping partners is also crucial for streamlining the logistics process and avoiding delays or errors. By prioritizing effective communication and coordination, you can improve the efficiency of your distribution network and provide reliable service to customers.
Establishing clear communication channels
Effective communication channels are crucial for successfully distributing stainless steel water bottles. Without proper communication, suppliers may not know when and where to deliver their products, leading to delays and missed deadlines. Thus, establishing clear communication channels is essential in optimizing logistics for stainless steel water bottle distribution.
To create effective communication channels, it's important to consider the following sub-lists:
- Assign specific points of contact: Designate a person or team responsible for communicating with suppliers and distributors. This'll ensure that information flows smoothly and efficiently.
- Use technology: Employ modern tools such as email, instant messaging apps, or project management software to facilitate communication between parties involved in the process.
- Establish protocols: Set up guidelines on how information should be shared and what type of data needs to be included in communications. This'll help avoid misunderstandings or confusion.
By implementing these strategies, you can build a solid foundation for effective communication and supplier collaboration that can streamline the distribution process of stainless steel water bottles.
Remember that clarity and transparency are key components of successful logistics operations, so aim to establish open lines of communication from the outset.
Coordinating with shipping partners
Coordinating with shipping partners can be a challenge, but it's essential for ensuring timely delivery of our products.
Partner selection is the first step in this process, as you want to work with reliable and efficient carriers who can handle your specific product needs. Factors such as cost, transit time, insurance coverage, and tracking capabilities should all be considered when choosing a shipping partner.
Once you've selected your partners, negotiation strategies come into play. You want to establish clear expectations and terms that are mutually beneficial for both parties. These negotiations should cover topics such as pricing, delivery schedules, handling procedures, and contingency plans for unexpected events.
By effectively coordinating with your shipping partners through careful selection and negotiation strategies, you can improve the efficiency of your logistics operations and ensure customer satisfaction.
Implementing Technology Solutions
By utilizing technology solutions, we can streamline our distribution process for stainless steel water bottles and improve overall efficiency. Here are three ways that technology can help:
- Automated inventory management - Implementing an automated inventory management system can save time and reduce errors in the distribution process. By using barcodes or RFID tags, warehouse staff can easily track the movement of each bottle through the supply chain. This helps to prevent stockouts and overstocking, ensuring that customers receive their orders on time while minimizing holding costs.
- Route optimization software - Planning delivery routes manually is a time-consuming process that may not always result in the most efficient use of resources. Route optimization software uses algorithms to calculate the best routes for multiple deliveries based on factors such as distance, traffic patterns, and delivery windows. This helps to reduce travel times, fuel costs, and vehicle wear-and-tear.
- Real-time tracking - Providing real-time tracking information to customers allows them to monitor their shipments from start to finish. This reduces anxiety about whether or not their package will arrive on time or if it has been lost in transit. Additionally, this solution allows companies to have full visibility into where packages are at any given moment, which aids in resolving issues quickly.
Implementing these types of technology solutions requires a cost-benefit analysis and consideration of implementation challenges such as training staff and integrating new systems with existing ones. However, with careful planning and execution, these solutions can help optimize logistics for stainless steel water bottle distribution while reducing operational costs and improving customer satisfaction levels.
Evaluating Performance Metrics
Tracking performance metrics is like using a GPS to navigate through the journey of improving our supply chain processes for stainless steel water bottle distribution. It's essential to measure efficiency and analyze data regularly to identify areas that need improvement.
This way, we can make informed decisions that impact our logistics operations positively. One important metric to track when evaluating the performance of our logistics operations is delivery time. Customers expect their orders to arrive on time, and if there are delays, it can result in dissatisfaction and loss of business.
By analyzing delivery times, we can pinpoint areas where bottlenecks occur and take steps to address them. Another crucial metric is inventory management. We must ensure we have enough stock at all times without overstocking, which could lead to unnecessary expenses.
Through careful analysis of data related to inventory levels, we can optimize the ordering process by setting reorder points based on demand patterns and avoiding stockouts or excess stock situations that affect customer satisfaction negatively. In conclusion, tracking performance metrics helps us make informed decisions about optimizing our logistics operations for stainless steel water bottle distribution effectively.
Continuous Improvement
Improving our supply chain processes for the distribution of stainless steel water bottles is an ongoing effort that requires a commitment to constantly refining and enhancing the way we operate. Measuring effectiveness is a crucial step in identifying areas for improvement. By tracking metrics such as delivery times, order accuracy, and inventory levels, we can identify patterns and trends that reveal opportunities for optimization.
To continuously improve our logistics operations, it's essential to gather feedback from all stakeholders involved in the process. This includes customers who receive our products, suppliers who provide raw materials, warehouse personnel who handle inventory, and transportation providers who deliver goods. By collecting input from these various sources, we gain valuable insights into what's working well and what needs improvement.
Identifying opportunities for improvement is only part of the equation - implementing changes based on those findings is equally vital. To ensure successful implementation of process improvements, it's essential to communicate changes with all relevant parties involved in the supply chain process. Clear communication helps mitigate disruptions and ensures everyone understands their role in making improvements possible.
With ongoing attention to detail and a commitment to continuous improvement principles, we can optimize logistics operations for stainless steel water bottle distribution while delivering exceptional customer service.
Frequently Asked Questions
What is the best way to clean stainless steel water bottles to ensure they remain in good condition?
To keep your stainless steel water bottles in good condition, use mild soap and warm water for hand washing or a gentle cycle on the dishwasher. Avoid harsh chemicals or abrasive scrubbers. Dry thoroughly and store with the lid off to prevent odor buildup.
How do you handle shipping delays or disruptions that may occur during the distribution process?
To mitigate disruptions in the distribution process, it's important to have contingency plans in place for shipping delays. This can include alternative shipping methods or routes, expedited shipping options, and clear communication with customers regarding any potential delays. Logistics optimization also involves regularly assessing and improving processes to reduce the likelihood of disruptions.
What is the most effective way to handle customer complaints or concerns about their water bottles?
To handle customer complaints or concerns about their water bottles, effective communication is key. Listen to their issues and offer solutions, such as product replacement. Address the problem promptly and provide excellent customer service.
How do you ensure that the distribution process is environmentally sustainable and responsible?
To ensure logistics efficiency and sustainable packaging, consider using eco-friendly materials and optimizing delivery routes. Reduce waste by implementing recycling programs and minimizing excess packaging. Regularly assess your processes for improvement.
What types of quality control measures are in place to ensure that all water bottles are in good condition before being shipped to customers?
To ensure customer satisfaction, packaging standards and quality control training are implemented to inspect each water bottle. Any defects or damages are addressed before shipment, avoiding any potential returns or complaints.
Conclusion
Congratulations! You've successfully optimized logistics for the distribution of stainless steel water bottles.
By following the steps outlined in this article, you've gained a deeper understanding of your customer base and their needs, effectively managed inventory, chosen the most appropriate shipping method, packaged and labeled products with precision, dealt with returns and exchanges seamlessly, communicated and coordinated efficiently among teams, implemented technology solutions to streamline processes, evaluated performance metrics regularly, and continuously improved your logistics system.
All of these efforts will not only enhance customer satisfaction but also increase profitability for your business. By prioritizing logistics optimization through a comprehensive approach that takes into account all aspects of the supply chain process from start to finish, you can ensure that your business stays ahead of the competition.
Remember to always keep an eye on emerging trends and adapt accordingly while staying true to your core values as a company. With continued dedication to excellence in logistics management practices, success is sure to follow.